When most people think about springs, they tend to have a specific image in their minds. Of course, a classic compression helical spring is the most well-known, but many other designs, such as flat springs, fulfil vital functions.
Flat springs may not resemble other springs, but they are used in a surprisingly broad range of applications, including automotive, aerospace, electrical, medical, and consumer product industries. Read on to discover why flat springs are effective for so many varied applications.
What Are Flat Springs?
The first thing to keep in mind is that flat springs don’t look like regular springs. Due to their distinct appearances, it may appear incorrect to classify these items as springs as they are made from flat metal strips. They will frequently resemble metal pressings and lack flexibility, but this rigidity is essential for generating the necessary energy storage to be considered a spring.
Metal flat spring pressings are formed into flat metal strips that, when compressed, stretched, or bent, can store and release energy. The stored energy is released when the constraining force is removed. These small parts are often put in places where control deflection is needed in tight spaces. As a result, these pressings are typically incorporated into larger mounting assemblies.
Materials Chosen for Flat Spring Applications
As flat spring manufacturers, we know the importance of choosing the right material when creating these springs for a specific application. Here are some examples of the materials we use during flat spring manufacturing.
- Carbon and Stainless steels: High carbon spring steel is an excellent choice for creating flat springs, resulting in a durable, high-strength spring suitable for many applications. It can be hardened and tempered to provide additional resistance to fatigue and wear, making steel an excellent choice for flat springs in industrial applications. Additionally, stainless steels avoid the need for corrosion protection and hardening and tempering. Bi-directional bends in stainless steel are limited due to grain direction within the material.
- Beryllium Copper: This non-ferrous alloy creates flat springs with high electrical conductivity. Electrical connectors and contacts benefit from this material whilst also getting a highly durable and strong flat spring.
- Phosphor Bronze: Flat springs made from this material have many of the benefits of the previous one but with the addition of increased corrosion resistance.
- Aluminium: Whilst aluminium is not commonly used for flat springs as it has low strength and low resistance, it is used for low-stress applications where weight is an immediate concern. These can sometimes be found being used as small springs for electronics.
Nickel Base Alloys For Flat Springs
Due to their resistance, nickel-based alloys are also utilised for flat springs intended to be used in high-stress and corrosive environments. Whilst these materials can be more expensive to create than alternative materials, they offer improved results. They are also more reliable, making them perfect for industrial machinery where each component must work efficiently. Here are some examples of nickel-based alloys used to create flat springs.
- Inconel is a nickel-chromium alloy that creates sufficiently strong flat springs with great technical properties. This material is used in foundries and other industrial manufacturing as it will have high temperature and corrosion resistance.
- Monel is a nickel-copper alloy often used in marine and chemical processing facilities due to the combination of high strength and corrosion resistance.
- Hastelloy combines nickel-molybdenum-cobalt into a single alloy that, when used for flat spring manufacturing, creates lightweight, strong and durable parts. You can find these in medical devices and aerospace applications.
- Nimonic is used worldwide in aerospace and gas turbine applications with its impressively high corrosion resistance and reliable strength and longevity. It is a combination of nickel-chromium-cobalt.
Examples of Flat Spring Applications
The previously mentioned applications are just a few different ways flat springs are used worldwide. Of course, this will include many specific tasks, like installing clips to hold car mouldings or minor contact points in electrical circuits.
Door Closers
Constant force springs involve coiling the pressing around themselves or a drum at a constant radius. Any presented load force will be resisted, similar to how an extension spring works. This design provides consistent torque regardless of the extension length, making it great for applications with a constant load, such as door closers, gym equipment, cable retractors and more.
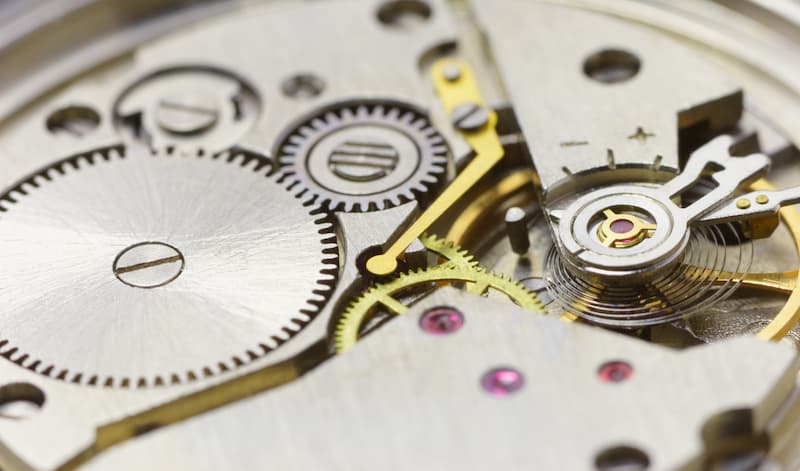
Clockwork Devices.
Clock springs are the oldest type of flat spring. These flat coiled springs are found in mechanical clockwork mechanisms, including older-style wristwatches. This classic miniature flat spring is usually made from a sheet of steel into a ribbon-style shape that is coiled tightly and compressed. The spring stores then release energy in the form of ticking hands. However, it needs regular winding to ensure it has a persistent energy store.
UK Flat Spring Manufacturing
Special consideration must be given when manufacturing flat springs and pressings, particularly custom designs. Many carbon and stainless steels will require treating, hardening or tempering after forming to ensure strength and corrosion resistance. Additionally, the conventions creation process (blanking) forms a sharp, rough edge (known as a burr) that mechanical deburring operations can remove. Small components may not lend themselves to this type of process, and consideration needs to be given at the design stage to the effects burrs might have on the component’s function.
Airedale Springs engineers have vast expertise in creating flat springs for various applications. Our team can even produce small sample batches of components ready for testing before resorting to the production of expensive tooling for bulk production.
If you are interested in our custom spring service or wire form manufacturing, contact us, and we’ll help you choose the best specification to meet your application’s needs.