Business resilience is an essential characteristic to develop, as building a strong collection of processes and protections will ensure your company will survive and even thrive when the unexpected happens. UK manufacturing has had to deal with many challenges, including a newly established term called ‘permacrisis’. Read on to learn what this means and how manufacturers like ours have overcome it and improved.
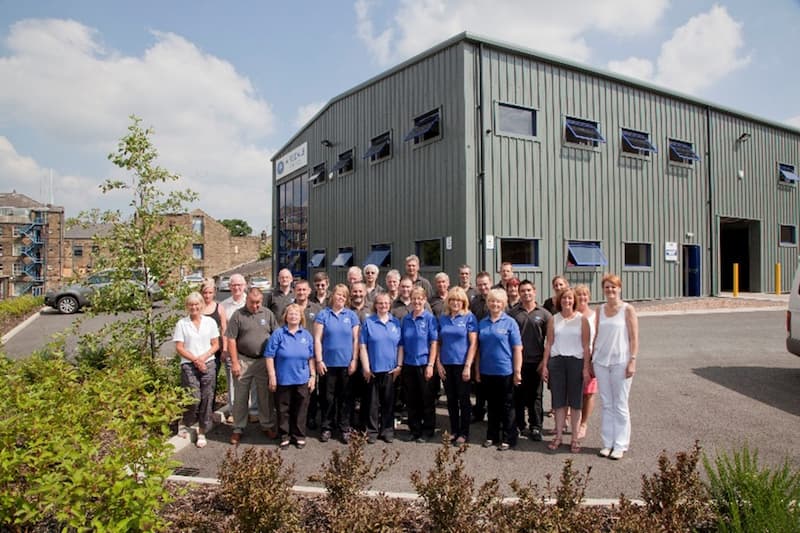
What is a Permacrisis?
A permacrisis is what our manufacturing industry here in the UK has been adapting to and overcoming for over five years. The word is a fairly new addition to the Collins English dictionary and has been defined as ‘an extended period of instability and insecurity’, something we are all familiar with due to the various national and global crises that have happened, such as Brexit, the Pandemic and Russia’s war in Ukraine and their impact on global supply chains.
The persistent problems that these challenges create for manufacturing have forced managers to build adaptive processes that can be easily adapted when outside events change the status quo. This is evident with the supply chain problems generated by the previously stated events and their continued disruptions.
Building a Resilient Manufacturing Process
Stability and reliability are the core aspects of resilient manufacturing, and we have seen that these have to be applied both externally and internally to have a lasting impact on our operations. In context, the internal element has addressed our processes for their material and energy usage, whilst the external factors relate to our interactions with our international supply chains.
Out of all the many considerations that meet these two categories, we’ve found the two most impactful: demand forecasting and local, renewable energy.
Demand Forecasting
Working with upstream supply chains means working with significant lead times and time constraints with forward planning to make sure your facility has everything it needs. Whilst this used to be easier in past years with stable, repeatable transit routes available for raw materials, spring manufacturers now need an adaptable process that will compensate for unexpected issues such as delays in shipping.
Demand forecasting is a successful tool for manufacturers to source expected material in advance and not only ensure its arrival in time but also reduce lead times and undercut our competitors. The general concept is quite simple: by analysing previous years’ activities, an estimation is created on what materials will be needed; this is especially useful when working with long-term clients whose specifications and designs you are familiar with. Any excess inventory is costly to store and maintain and is an inefficient use of valuable expenses and resources that could be put to better use. Improved inventory management with demand forecasting ensures businesses have the suitable materials to meet customer demand without unintentionally being inefficient with their assets.
Investment In Renewable Energy
Manufacturing has high energy needs, and fulfilling this need will have a significant impact on a company’s expenses with the increases in energy costs in the UK. Additionally, the increased costs can seem pointless when rolling blackouts halt your facility’s operations erratically and ruin productivity. The best resilient solution we’ve found for this is to invest in locally generated power through renewable energy sources.
We currently have 438 solar panels installed onto our facility’s roof. We have slowly installed these over time, and now, we benefit from over 80% of our annual energy needs being fulfilled by this reliable and renewable source. Additionally, we have a 192Kw battery storage centre onsite that holds the surplus energy generated and can even run our entire facility for over four hours on its own.
Our chairman, Tim Parkinson, has this to say about this green initiative. “We’ve decided on the back of continuing increases in energy to extend the system with the aim of getting off the grid as much as possible. That is a two-pronged approach. The first is to increase our ability to generate more electricity using the existing and additional panels, which also have a battery backup system. The second is to reduce our electricity use as part of improvements being made to our manufacturing processes.”
Our commitment to this plan to develop a sustainable and energy-resilient facility is clear as we let our fixed-term energy contract end in October 2023. “Even though we’re paying more for our electricity, our actual usage will be more manageable. But we’re still predicting our energy expenditure year-on-year to increase. So it’s about trying to mitigate a bad situation rather than making money out of the process,” Tim explains.
“From the prices we’ve been quoted, our electricity bill will increase by £100,000 a year over what we paid in 2022. To install the solar panels will be £300,000, which is a big investment for a small business like ours, but if we can reduce that £100,000 even by 50%, the new solar system will have paid for itself in six years. So we either decide to spend £100,000 extra on electricity and do nothing, or we make that investment. For us, it’s a bit of a no-brainer.”
Reliable Spring and Wire Form Manufacturing From Airedale Springs
To support our goals to grow Airedale Springs further, we are exploring new areas of investment and expansion whilst not compromising our company’s resilience. Here are Tim’s thoughts on the coming year. “We’re probably heading into a recession this year, which will be my sixth over my working career. The good news is that they do eventually come to an end, but to ensure you’re one of the businesses still standing, you have to stay ahead of the game by investing in people and equipment.”
Contact us to choose a reliable industrial spring manufacturer that has proven its resilience to any new challenges our economy is exposed to.