Non-ferrous metals and alloys are called so because they lack the iron content that ferrous materials have. Choosing the right materials for springs is critical, since they will impact the quality and longevity of the final product. At Airedale Springs, we work with both ferrous and non-ferrous metals, which are used in different situations.
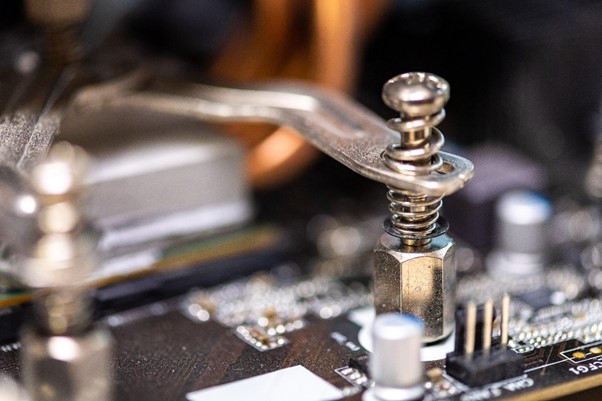
Spring materials will depend on the end use of the spring. For example, in the electronics sector, it’s important that the metals are strong, conductive and with good resistance to heat and corrosion. This is why copper, a non-ferrous metal, is so popular for this industry- not just for its technical properties but also for its ability to be reused in the future, making it a responsible choice for industries prioritising environmental goals.
There are many other non-ferrous materials in spring manufacturing, such as the ones we’re highlighting in this article.
Why Use Non-Ferrous Materials for Springs?
There are many different types of non-ferrous materials, many of which are used to make springs and wire forms. Although they’re all different, they share similar characteristics, such as high resistance to corrosion, easy machinability, good weldability, great thermal and electrical conductivity, lower mass than ferrous metals, and non-magnetic properties.
Non-ferrous springs may not be as strong as materials with iron content in their composition – and they may be more susceptible to fatigue as well – but they also provide the ductility and resistance to extreme temperatures that ferrous metals and alloys may not have. Additionally, non-ferrous metals, like aluminium and copper, are valued for their recyclability and lower environmental impact, helping manufacturers reduce waste without compromising performance.
Aluminium
This metal is widely used in spring manufacturing, including in its alloyed forms. By itself, aluminium is malleable and not as strong as other materials – by adding other metals and putting it through specific treatments, aluminium can achieve the necessary properties. Cold working aluminium can increase its hardness, meaning it needs annealing.
Aluminium is a lightweight metal (2.7g/cm3, which is around a third of the weight of steel) and resistant to corrosion, so it’s often used in industries where this is a concern, like aerospace, marine and rail. Its lightweight nature contributes significantly to sustainability in these sectors by reducing the overall energy consumption of vehicles and structures. Aluminium also reflects radiant energy and is non-magnetic, and its melting point is 660.32oC. This metal is also non-toxic and doesn’t splinter.
For manufacturers focused on reducing their environmental footprint, aluminium offers the advantage of being one of the most widely recycled materials globally, with recycling requiring just 5% of the energy used in primary production.
At high temperatures, aluminium alloys tend to lose some of their strength, although they are good for electrical applications, since they have high electrical conductivity. Popular alloys include the addition of magnesium and manganese (which adds strength and allows for malleability) and magnesium and silicon (which produces strong but lightweight parts).
You can find aluminium springs in a wide range of applications, including bicycles, aircraft, door mechanisms, motors and generators.
Copper
As spring manufacturers, we work with a variety of industries at Airedale Springs, and each of them has its own specific requirements. For this reason, it’s important that we understand how materials can impact the end product. Copper, as we mentioned, is great for electrical applications, so it’s one we use for springs in that sector.
This metal is a popular non-ferrous material. If it’s not alloyed with any other metal, copper is soft and ductile; with the addition of the other metals, copper’s mechanical properties are boosted.
Common alloys are beryllium-copper, which is easy to weld and machine, and is also resistant to wear and tear, and brass (when zinc is added to copper). Brass is resistant to corrosion due to the zinc addition, an element with many different applications that is often used to galvanise steel in a variety of fields. In regard to resistance to corrosion, copper also reacts with oxygen to form a layer of copper oxide that protects metal from corrosion.
The main applications of copper are electrical, but the metal and its alloys are also found in roofing, industrial machinery, musical instruments and even in agriculture. In regard to springs made from copper and/or other alloying elements, they are common in electronics as well, but can also be found in valves, engines and tools. Copper’s ability to be endlessly recycled without losing its properties makes it a standout choice for manufacturers looking to meet both performance and environmental targets.
Nickel
This metal is also commonly used in spring manufacturing. This silvery-white metal is everywhere around us, from batteries to electric guitar strings. Known for its toughness, resistance to corrosion and resistance to extreme temperatures, nickel is also an incredibly versatile material that can be alloyed with a large number of metals.
Durable and strong, nickel alloys are ideal for environments such as those found in oil rigs and chemical plants, and they’re reliable for indicating instruments as well. Cobalt-nickel is a popular alloy, often chosen when the strength of stainless steel is not enough for a specific use; the alloy is not just strong, but durable, ductile and highly resistant to wear and to corrosion.
Nickel alloys are not only valued for their performance but also for their contribution to sustainability. Nickel is recyclable and often reused in the production of new alloys, reducing the demand for raw material extraction. Other alloys include nickel-iron, nickel-copper and nickel-chromium, and all of which are suitable for low and high temperatures.
Nickel and its alloys are easy to shape and machine, so they are sought-after for springs as well. They tend to have good solderability and thermal conductivity and can also be resistant to chemicals and caustic materials. These springs are used for aerospace components, food manufacturing processes, and electronic products.
How We Can Help
Non-ferrous materials like the ones we talked about are typically used in electrical applications due to the non-magnetic nature of these metals and alloys. However, as compression spring manufacturers, we are able to produce a vast array of springs made from both ferrous and non-ferrous metals. By incorporating materials like aluminium, copper, and nickel, we not only meet the technical demands of modern industries but also contribute to more sustainable manufacturing processes.
You can contact us to discuss your project with us or to ask us any questions about our processes and materials. We are also easy to reach on sales@airedalesprings.co.uk and on 01535 643456.