Sustainability is a crucial focus of the manufacturing sector, with many new processes, initiatives and systems in place to create a greener industry. Creating a more eco-friendly business is a challenging transition but one that many manufacturers, such as ourselves, are achieving with dedication and innovation.
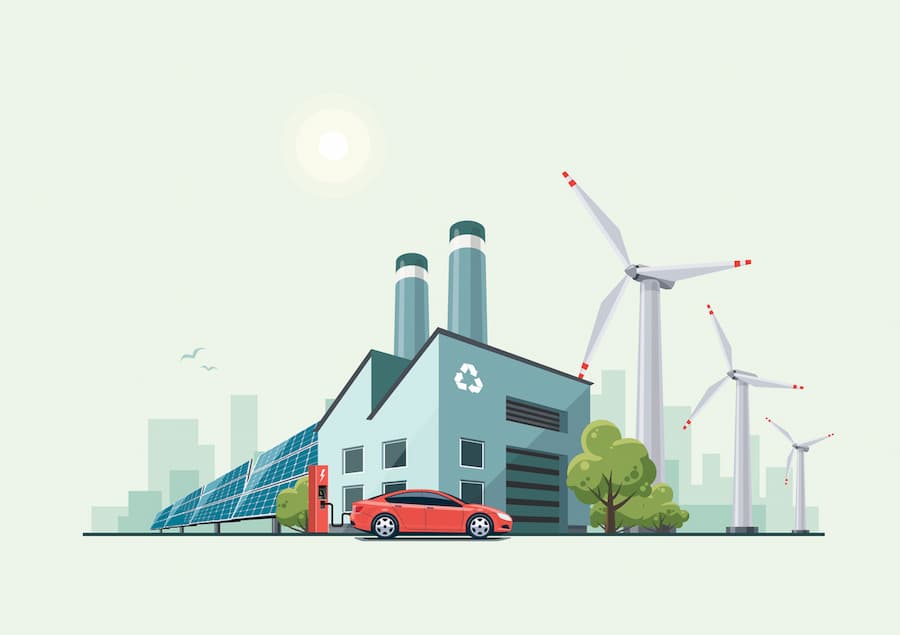
What Is Green Manufacturing?
Otherwise known as the green industrial revolution or sustainable industry, green manufacturing is a broad title addressing industries’ need to reduce their environmental impact. The essential goal of green manufacturing is to make positive changes related to its environmental impact within the manufacturing industry.
Pursuing green manufacturing means investing in renewable production methods and lean use of resources. These goals can be achieved through various solutions to meet each facility’s needs, but all manufacturers follow similar goals.
Elements of Green Manufacturing
- Renewable energy implementation and support
- Increased energy efficiency
- Reduced pollution and waste
These common goals apply to the manufacturing industry as a whole, but what are some of the methods companies are using to get there?
Energy Efficient Manufacturing
Improved energy efficiency is an element that is pursued both inside and outside of green manufacturing. Improving your facility’s energy usage reduces your expenses and the environmental impact of your energy consumption.
To achieve this target of becoming a green manufacturer, one of the vital factors to address is energy usage. As spring manufacturers, we know that our industry is energy-intensive, with most being used for production processes. Because this energy usage is within the facility, it provides managers with many areas where they can reduce it with energy-efficient improvements.
Monitoring Energy Usage
Monitoring usage; compiling the data of a facility’s energy usage from all the varied areas provides managers with a clear image of where energy is used most. This data can be broken down by installing individual meters in specific areas or even on machines to reveal wasted energy. Knowing where improvements can be made is the first step to improved energy efficiency.
Lean Energy Use
Limiting energy to just the essential processes has reduced energy usage significantly. This concept can be implemented by encouraging staff to turn off computers or other electronics when not in use. Additionally, many facility managers are investing in adaptive, motion-activated lighting that will only draw power in an area being worked in. This same concept can be extended into manufacturing equipment, with machines only activated during the day.
Adaptive Heating and Cooling
Both heating and cooling can be customised within manufacturing facilities to suit the season, and this maintains a pleasant temperature without wasteful excess. For example, timer controls can be installed in environmental systems so they can only activate in areas which are in use. Additionally, maximising natural ventilation reduces the need for artificial cooling, which is detrimental to the environment.
Investing in Renewable Energy Sources
Investing in renewable energy is an increasingly popular method of carbon offsetting for manufacturing. Unfortunately, some manufacturing companies are unable to install renewable energy solutions. Still, they can purchase carbon offsets that support their development alongside other systems, such as carbon capture units. Carbon capture is a system to draw harmful particles from the air and eliminate their detrimental impact. Each carbon offset represents a metric ton of C02 (carbon dioxide).
With manufacturers helping to develop these schemes, there is a future where minimal carbon emissions are compensated to create a neutral, green industry.
At Airedale Springs, we excel at reducing our energy consumption despite the energy-intensive nature of our work as wire form manufacturers. We are one of the few manufacturers to be rated A thanks to our various green initiatives, such as:
- Investing in energy-efficient LED lighting
- Installing advanced compressed air systems that use 40% less power than basic alternatives
- Attaching 132 solar panels to our facility’s roof powers 20% of our building’s electrical consumption alone.
Efficient Material Use
The energy required to source raw materials is also considerable but, unfortunately, will remain costly in both financial expenses and energy usage. As a result, manufacturing is now focusing on using recycled materials available as efficiently as possible and making sourcing raw materials almost a last resort.
The industry invests heavily in recycled materials for new manufacturing processes to reduce waste while eliminating the need for new materials. This choice has significant additional bonuses as recycled materials are generally sourced locally and do not need to be transported internationally through unpredictable supply chains. Recycled materials are also cheaper to acquire in terms of energy and expenses than sourcing new materials.
With newly sourced materials, most companies use lean manufacturing techniques to use most of their valuable resources and vastly reduce waste, which is reduced further with effective recycling.
Sustainable Manufacturing
Airedale Springs is committed to meeting our green manufacturing goals and being a profitable member of a more ecologically friendly manufacturing industry. As the leading small spring manufacturers in the UK, we feel a profound responsibility to promote more sustainable manufacturing techniques from our award-winning facility. Contact us if you have any questions about our green manufacturing methods or the various designs of springs and wire forms we make with them.