Choosing the best spring material and finish is crucial for ensuring optimal performance and longevity of compression springs in various applications. Essentially, the material of the spring determines its mechanical properties, such as strength, elasticity, and durability, whilst the finish will provide essential protection. Read on to explore our guide on compression spring materials and finishes and know which you need for your next application.
Choosing the Best Material
The choice of compression spring material and finish depends on the specific application requirements, such as the load the spring will be subjected to, the temperature range it will operate in, and the environment it will be exposed to.
For example, if the spring is used in a high-temperature application, a material like Inconel may be chosen for its high-temperature strength and resistance to oxidation. Similarly, it is used in a corrosive environment; a finish like electroless nickel plating may be applied to protect the spring from corrosion.
By understanding the application requirements for spring design, engineers will choose the best compression spring materials and finishes to ensure optimal performance and longevity.
Compression Spring Materials
There are many popular choices for compression springs, and each material has its own unique properties that make it suitable for specific applications; these include:
- Steel alloys (e.g. music wire, chrome silicon, chrome vanadium)
- Stainless steel (e.g. 302, 316)
- Titanium (e.g. Ti-6Al-4V)
- Nickel alloys (e.g. Inconel, Hastelloy)
- Phosphor bronze
- Beryllium copper
- Brass
- Copper alloys
- Aluminium alloys
- Plastics (e.g. nylon, PTFE)
The correct choice of material for a compression spring depends on the specific application requirements and finding the material with the appropriate properties to meet them. Here are two of the above examples’ properties.
- Steel alloys are often used for compression springs due to their high strength and durability. However, stainless steel is also popular due to its corrosion resistance and ability to withstand high temperatures. Both are used widely in machinery where they will be subjected to significant stresses.
- Titanium is a lightweight and strong material often used in aerospace and medical applications. Nickel alloys, such as Inconel, are known for their high-temperature strength and resistance to corrosion.
In the automotive industry, high-strength steel alloys are often used for suspension springs due to their ability to withstand heavy loads. However, nickel alloys like Inconel are chosen in aerospace applications for their high-temperature strength and resistance to oxidation. In medical devices, biocompatible materials chosen by small spring manufacturers like titanium ensure compatibility with the human body.
Compression Spring Finishes
Spring finishes refer to the coating or treatment applied to the surface of a compression spring. These finishes are an important addition as they protect many external elements that would reduce the lifecycle of your spring components, such as corrosion, wear, and fatigue. Several types of spring finishes are available, including plating, painting, and powder coating.
Spring Plating
Plating involves applying a thin layer of metal, such as nickel or chrome, onto the surface of the spring to improve its durability and resistance to corrosion. Here are examples of plating used to protect springs.
- Zinc plating – Provides corrosion resistance and improves the aesthetic appearance of the spring.
- Nickel plating – Offers excellent corrosion resistance and wear resistance, making it suitable for harsh environments.
- Chrome plating – Provides a hard, durable surface resistant to wear and corrosion.
- Gold plating – Offers a decorative finish and is often used in jewellery and other high-end applications.
Spring Painting
Painting is a popular spring finish that involves applying a layer of paint onto the surface of the spring to protect it from environmental factors like moisture and dirt. This aesthetic finish also offers several benefits for spring manufacturers and applications. Painting is a cost-effective finish that protects the spring from the elements and improves its appearance if the application has the spring externally visible such as consumer goods.
Spring Powder Coatings
powder coatings are a popular finish for compression springs as they provide a durable and long-lasting protective layer. This finish involves applying a dry powder coating onto the surface of the spring and then curing it with heat to create a hard, protective layer.
Powder coatings offer several benefits over other types of finishes. They provide excellent resistance to corrosion, wear, and impact, making them suitable for use in harsh environments. Additionally, powder coatings offer a uniform and consistent finish, which is particularly important for complex-shaped springs.
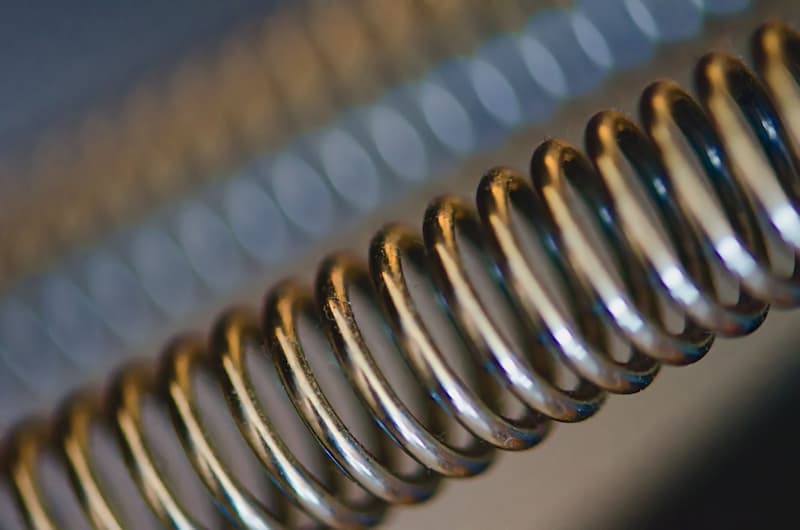
Additional Finish Choices
In addition to the previously mentioned spring finishes, there are other alternatives available that offer unique benefits.
E-coating provides a uniform and corrosion-resistant finish that is suitable for complex-shaped springs. It involves applying an electrically charged coating onto the surface of the spring, which creates a uniform layer that is resistant to corrosion.
Black oxide is another finish that provides a decorative black finish while offering some corrosion resistance. This finish is achieved by immersing the spring in a hot solution of black oxide, which forms a thin layer of black oxide on the surface of the spring.
Passivation is a process that removes free iron and other contaminants from the surface of the spring to improve corrosion resistance. This is achieved by immersing the spring in an acid solution that removes the contaminants and creates a passive oxide layer on the surface of the spring.
Anodizing provides a hard, durable surface that is resistant to corrosion and wear, making it suitable for aerospace and military applications. This finish involves immersing the spring in an electrolyte solution and applying an electric current, which creates a hard oxide layer on the surface of the spring.
Custom Compression Spring Manufacturer
Each type of material and finish have its own benefits, and making the right choice is essential to ensure the longevity of your application. At Airedale Springs, we have decades of experience as a custom compression spring manufacturer and have provided high-quality products for applications across every sector and industry. Contact us to discover how our custom compression spring design and wireform service will benefit your next application.