Predicting the way technology will progress in the future is a challenge. However, it’s not far-fetched to say that the latest technologies, like automation, are opening the door to a new era in global manufacturing.
Automated tools like robots and AI are not just the latest tools in factories and warehouses around the world – they’re essential elements of modern manufacturing. Below, we discuss how automation is changing the face of the industry and how it will impact it in the future.

1. Automation and the Evolution of Jobs in Manufacturing
Although automation is an exciting concept, it is understandable that some manufacturers have concerns. One of the most significant concerns regarding automation is its impact on jobs. While fears that robots and AI will replace human workers are common, the reality is more complex. Automated robotics are used to strengthen our economy by taking over repetitive and dangerous tasks in manufacturing and letting our experienced human engineers move to more interesting and complex tasks in their field. This efficient use of labour also closes many gaps that have formed with the low numbers of new engineers joining the sector each year.
For instance, while up to 30% of existing UK jobs could be automated by the early 2030s, these roles are more likely to evolve than vanish. Employees will increasingly focus on complex problem-solving and supervisory tasks, areas where human input is essential. The key to navigating this transition in manufacturing, we’ve found, is in educational awareness of how these systems will benefit the workplace, as well as training for technicians to be able to oversee these systems and monitor their automated operation.
Boosting Productivity Through Automation
Automation is a key driver of increased productivity in manufacturing. It reduces manual delays, minimises human error, and accelerates time-consuming tasks, leading to a more streamlined and efficient production process.
In addition to speeding up operations, automation enhances safety by reducing the risk of workplace injuries, which can further disrupt production. Automated systems can maintain a consistent level of output, allowing businesses to meet high demand without compromising on quality. As a result, manufacturers can focus their human resources on strategic activities that add value to the business, driving overall growth and competitiveness.
2. Building a Flexible and Resilient Supply Chain Through Automation
We have all experienced global events this decade that made us question the strength of our supply chains, and we feel that automation offers a way to mitigate risks and ensure continuity against any future unforeseen events.
Automation also supports and optimises supply chains, both up and downstream, surrounding manufacturing facilities themselves. By automating various elements of the supply chain, such as tracking logistics, inventory management, and order processing, manufacturers can achieve faster delivery times, lower costs, and improved accuracy. This level of efficiency is particularly vital in today’s fast-paced market, where meeting tight deadlines without sacrificing quality is essential.
By automating inventory management, order processing, and logistics tracking, manufacturers can maintain a steady flow of materials and products, even in the face of disruptions. Automation also supports supply chain resilience by enabling more accurate forecasting and demand planning.
With the ability to analyse vast amounts of data in real time, automated systems can predict potential disruptions and suggest alternative strategies to maintain operations. This level of preparedness is essential for manufacturers looking to navigate an increasingly complex global market.
Additionally, automated supply chains allow businesses to implement strategies such as nearshoring, which involves sourcing materials from regional suppliers to reduce reliance on international logistics. This approach not only minimises the risk of supply chain disruptions but also allows for greater control over inventory and production schedules. By investing in automation, manufacturers can create a more flexible and resilient supply chain capable of withstanding the challenges of a rapidly changing world.
3. Smart Factories: The Next Step in Manufacturing Evolution
Smart factories represent one of the most significant advancements in the manufacturing industry, driven largely by automation. A smart factory integrates digital technologies across the entire production process, resulting in a highly efficient and adaptable system. At its core, a smart factory relies on the continuous collection and sharing of data through interconnected systems, allowing for real-time monitoring and optimisation of operations.
The key components of a smart factory include big data analytics, cloud computing, and the Industrial Internet of Things (IIoT). These technologies work together to create a comprehensive management system that can self-optimise, reduce downtime, and enhance overall productivity. For example, smart sensors installed throughout a factory can monitor machine performance, detect potential issues, and trigger automatic adjustments to prevent disruptions. This proactive approach ensures that production runs smoothly, even in complex manufacturing environments.
As more spring manufacturers adopt smart factory technologies, our industry is moving toward a more digital and interconnected future. This shift improves operational efficiency and allows for greater customisation and flexibility in production. Businesses that embrace the smart factory model, stay competitive in an increasingly automated world and better meet the demands of their customers.
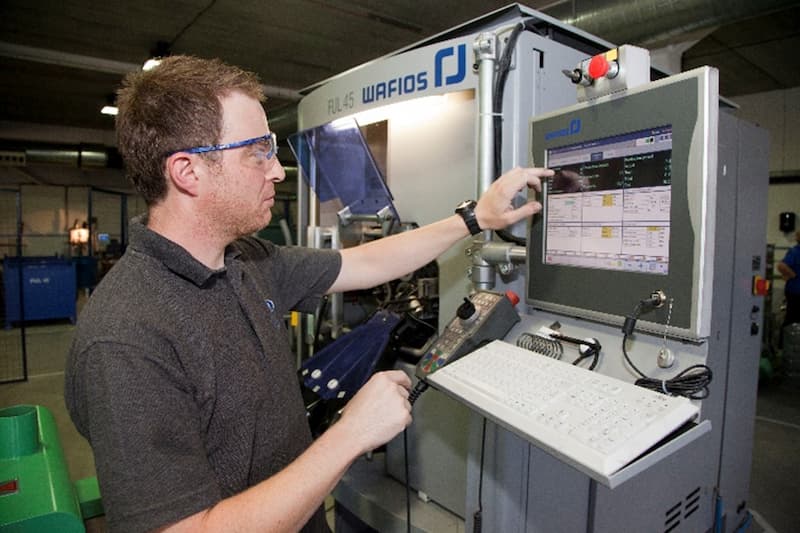
Airedale Springs Embracing the Future of Manufacturing
Automation is undoubtedly transforming the manufacturing industry, offering both challenges and opportunities in spring design and manufacturing.
Our dedication to excellence has led to numerous accolades and awards, solidifying our reputation as a trusted provider in the industry. When manufacturing high-performance springs, our rigorous quality control processes set us apart. We take pride in our track record of exceptional service, ensuring that each spring meets stringent quality standards.
Contact us today to discover how we can support your spring manufacturing needs and drive your designs forward with our advanced systems and processes.